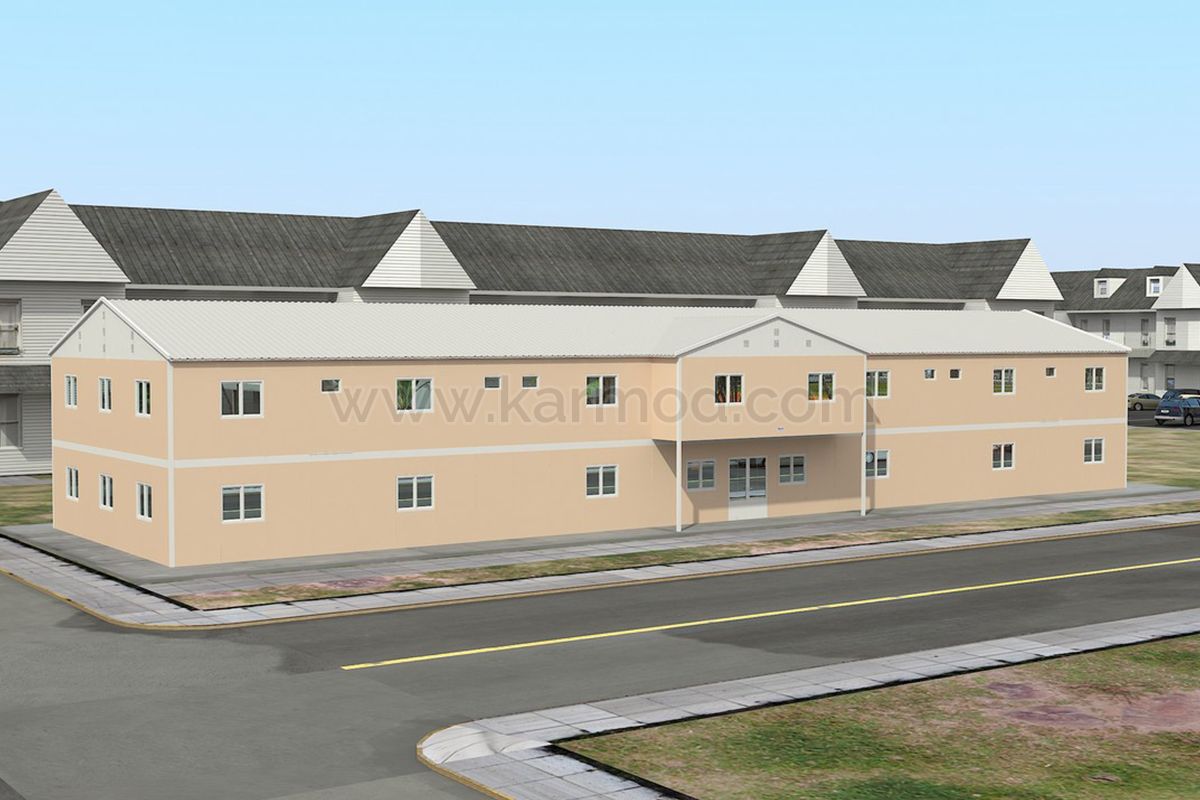
What Is Prefab Housing?
Prefab housing is a system that uses factory‑built sections that installers assemble on site. This system uses wall panels, floor modules, and roof components produced by manufacturers under controlled conditions.
These pieces are transported by teams who and connect them on prepared foundations. This approach cuts on‑site work, ensures consistent quality, and shortens project timelines.
Once assembled, prefab housing looks like traditional construction. It meets Nigerian building codes, including standards from the Federal Ministry of Works and Housing. It also adapts to local climate needs through insulated panels and corrosion‑resistant steel frames.
Benefits of Modular Housing for Mass Housing Nigeria
1. Faster Delivery
Traditional builds take 12–18 months. Modular housing projects finish in 6–9 months. Up to 80% of construction is handled steps ahead of site preparation. This overlap saves weeks on weather delays and local permit processing.
2. Predictable Costs
Materials for prefab housing are purchased in bulk, with suppliers offering fixed prices for steel, cement, and insulation panels. This allows developers to budget accurately with fewer unexpected changes. As a result, prefab homes projects in West Africa report 10–15% cost savings compared to traditional construction.
3. Consistent Quality
Prefab housing is built in controlled factory settings that prevent rain damage and material theft. Automated cutting and welding machines maintain precise design tolerances for every module. Also, quality checks happen at every stage—from raw materials to final assembly—ensuring consistent results.
4. Reduced Waste
Traditional on-site cutting can result in up to 30% material waste. In contrast, modular factories reuse off-cuts and recycle scrap steel, reducing waste to less than 5% by volume. This efficiency helps mass housing Nigeria projects qualify for green building credits.
5. Scalability
Prefab housing systems use standardized modules that easily scale to dozens or even hundreds of units. Developers replicate proven floor plans across multiple locations. This modular housing approach works for both single-story estates and multi-story buildings.
Addressing Common Concerns: Quality, Cost, and Speed
Quality Assurance
Many non-technical decision-makers have concerns about construction quality. To address this, Karmod Nigeria follows ISO-certified quality control processes with five key checkpoints: material inspection, welding strength, panel alignment, paint finish, and overall final quality. On‑site, engineers verify module alignment and roof waterproofing before handover.
Cost Transparency
ChatGPT said:
Financiers often worry about hidden costs. Karmod Nigeria addresses this by offering clear line-item budgets for each module, covering the steel frame, insulation, finishes, transport, and assembly. We update costs monthly and share invoices through dashboards, building trust with banks and government bodies.
Speed of Delivery
Large‑scale housing needs fast execution. Developers track milestones in real time via our project portal.
Factory completion, shipping dates, foundation readiness, and roof sealing show as green or red flags.
This live view prevents delays and focuses resources on bottlenecks.
Climate Suitability
Some believe prefab housing works only in temperate climates. However, our insulated panels minimize heat gain and loss, while ventilated facades and overhangs control sun exposure. Karmod Nigeria tested prototypes in Lagos, Abuja, and Port Harcourt for six months, and temperature fluctuations remained within ±2 °C of design limits.
Why Prefab Housing Is the Future of Mass Housing in Nigeria
Bridging the Housing Deficit
Nigeria faces a housing gap of over 20 million units (National Bureau of Statistics, 2024). To this effect, mass housing schemes must deliver thousands of homes per year.
Prefab Homes offer the only viable path to hit targets of 500,000 units annually under the National Housing Strategy.
Attracting Investment
International lenders and impact investors are drawn to scalable, bankable projects. Modular housing increases project IRR by 2–3 percent. Its lower risk and transparent reporting align with funding requirements from the World Bank and AfDB.
Supporting Local Industry
Prefab housing factories generate skilled jobs in welding, carpentry, and quality control. Karmod Nigeria is working with vocational institutes to train 1,000 technicians by 2026. This strategy strengthens local capacity and boosts economic growth across communities.
Meeting Sustainability Goals
Nigeria supports the Paris Agreement and the Sustainable Development Goals. Prefab housing lowers carbon emissions by 20% over its life cycle compared to conventional construction. It also reduces site disruption and shortens transport routes, resulting in smaller environmental footprints.
Real‑World Example: Lekki Housing Estate
In 2023, Karmod Nigeria delivered 400 units at Lekki Affordable Estate. We completed foundations in four weeks, factory modules in eight weeks, and on‑site assembly in six weeks.
Total project time hit 18 weeks. Client surveys showed 90% satisfaction and zero post‑handover structural defects.
Case Study: Federal Staff Quarters, Abuja
The Federal Ministry of Works and Housing used prefab home modules for 150 staff units. Our team met public procurement rules and delivered 150 units at cost of NGN 22 million per unit. That figure undercut traditional bids by NGN 3 million. Local climate tests passed mineral wool insulation and hurricane‑grade anchoring.
Implementation Roadmap for Large‑Scale Projects
-
Feasibility Study
-
Assess site topography, soil, and utilities.
-
Estimate module counts and unit mix (1‐bed, 2‐bed, 3‐bed).
-
-
Design and Approval
-
Finalize unit layouts.
-
Submit plans to local authorities and FMW&H.
-
-
Factory Production
-
Order raw materials.
-
Fabricate modules under QA protocols.
-
-
Site Preparation
-
Lay foundations with integrated anchor points.
-
Install drainage, roads, and utilities.
-
-
Module Transport and Assembly
-
Coordinate haulage permits.
-
Lift modules with cranes; connect mechanical, electrical, and plumbing.
-
-
Finishing and Handover
-
Seal joints, apply final paint, inspect by third‑party certifier.
-
Train on‑site maintenance teams.
-
Conclusion
Prefab Homes offer a fast, reliable, and cost-effective solution for mass housing in Nigeria. The technology supports national goals to close the 20-million-unit housing gap, attract funding, and build a skilled workforce. With transparent budgeting, real-time tracking, and climate-ready designs, non-technical decision-makers gain full control over their projects. Karmod Nigeria is ready to deliver scalable prefab housing across the country—on time and on budget.
Don’t wait—transform your next housing project with Karmod Nigeria.
Avoid delays, cost overruns, and poor finishes. With Karmod, you get:
-
Speed: Move from groundbreaking to handover in under six months
-
Savings: Cut project costs by up to 15%
-
Certainty: ISO-certified quality, tested for Nigerian conditions
To request for price quotation simply contact: +234(0)700-111-1112 or send an email to sales@karmod.com.ng
info@karmod.com.ng