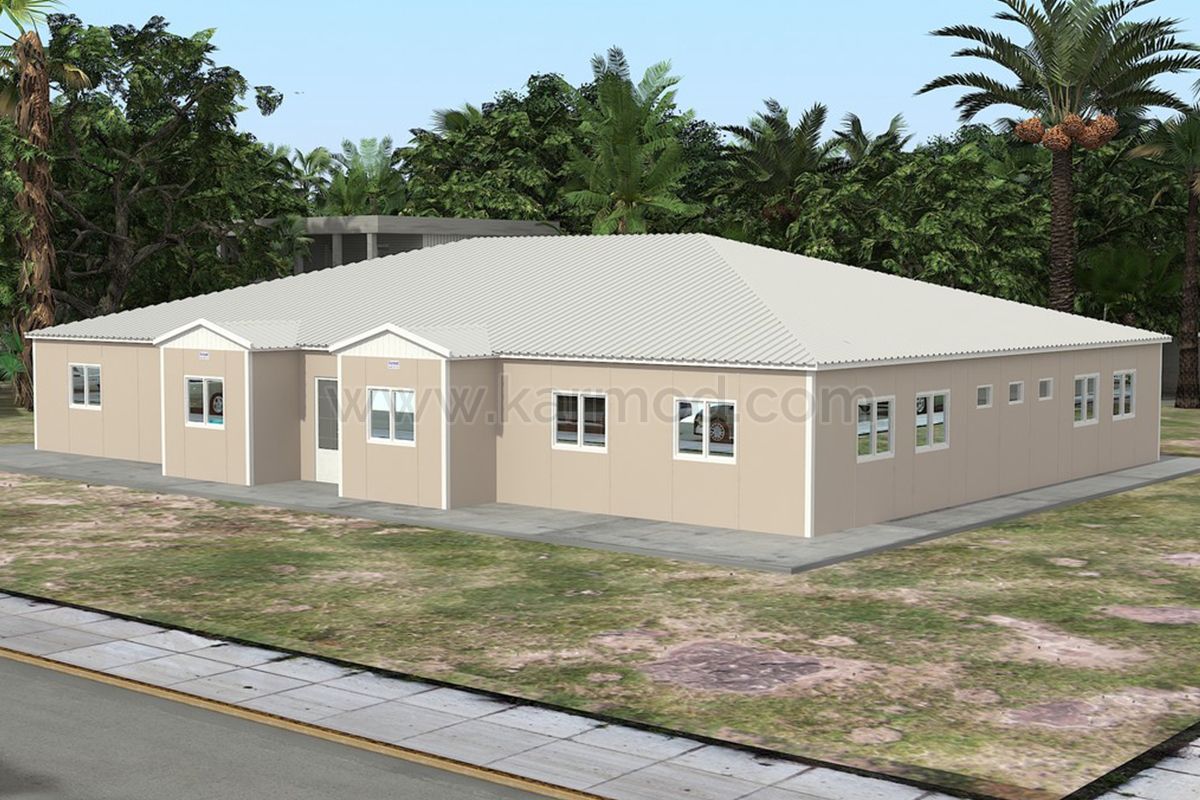
In Nigeria’s growing housing market, cost remains a top concern for decision‑makers. Rising material prices, labor shortages, and tight timelines put pressure on budgets. Prefab Homes offer a clear path to lower expenses without sacrificing quality. This article breaks down real costs, explains process control, highlights scale benefits, covers financing options, and shares local success stories. Read on to see why Prefab Homes could be the smarter, cheaper choice for your next mass housing project.
Prefab Homes Cost Breakdown
A transparent cost comparison helps you see savings at every step. Below is a simplified line‑by‑line estimate for a 100‑unit, 50 m² mass housing project in Lagos:
Cost Component | Traditional Build (₦/unit) | Prefab Homes (₦/unit) | Savings (₦/unit) |
---|---|---|---|
Materials (blocks, cement) | 2,000,000 | 1,400,000 | 600,000 |
Labor (on‑site) | 800,000 | 400,000 | 400,000 |
Transport (truck haulage) | 200,000 | 150,000 | 50,000 |
Site Prep & Foundation | 300,000 | 250,000 | 50,000 |
Waste Disposal | 100,000 | 40,000 | 60,000 |
Total per Unit | 3,400,000 | 2,240,000 | 1,160,000 |
On a 100‑unit scale, prefab cuts total project cost by over ₦116 million. Savings come from bulk material ordering, controlled factory labor, and reduced rework on site.
Prefab Homes vs. Brick‑and‑Mortar Labor Costs
Skilled masons and carpenters command premium rates in Nigeria’s hot market. Traditional builds often stall when workers chase higher pay.
Prefab Homes shift most labor offsite in a factory setting. Your benefits include:
-
Wage inflation. Rates can jump 10–15% mid‑project as workers switch to higher‑paying sites.
-
Unreliable attendance. Crew members juggle multiple projects, leading to stalled work when they shift focus.
-
Lengthy schedules. Building walls, roofing, and finishing can take 4–6 weeks per unit, even for experienced teams.
Prefab Homes solve these issues by moving about 70% of labor to a controlled factory setting. Here’s how you benefit:
-
Lower hourly rates: factory workers earn 15–20% less than on‑site masons because the assembly line setting boosts efficiency and reduces skill‑premium pressures.
-
Consistent staffing: you secure dedicated teams for each production phase. Factory crews don’t chase side gigs, so you avoid idle days and keep your project on track.
-
Predictable timelines: a trained prefab crew can erect walls and roofs in 2–3 days per unit. You lock in delivery windows, eliminating weather delays and weekend downtime.
-
Reduced overtime costs: off‑site scheduling absorbs peak‑demand labor needs, so you rarely pay double‑time for urgent shifts.
-
Fewer contractor markups: subcontractors can’t layer high emergency fees when you control the production pipeline under one roof.
By shifting four out of every five labor hours off‑site, you cut direct labor costs nearly in half. You also gain cleaner sites, safer working conditions, and faster approvals from local authorities.
This streamlined labor model makes Prefab Homes a clear winner for large‑scale, cost‑sensitive housing projects.
Prefab Homes Time Savings for Mass Housing
Time is money. Delays on site carry daily overhead: site security, equipment rentals, and management fees. Prefab Homes compress your schedule through parallel workflows:
-
Factory production runs concurrently with site preparation.
-
Just‑in‑time delivery ensures modules arrive as foundation work finishes.
-
Simple assembly lets you stack units quickly, even in poor weather.
For a 100‑unit estate, you can finish structural assembly in 8–10 weeks, compared to 24–30 weeks traditionally. A shorter timeline slashes holding costs and lets you start rentals or sales sooner—boosting your return on investment.
Prefab Homes Quality Control and Waste Reduction
In a controlled factory environment, you maintain strict standards for every panel and module. Key quality advantages include:
-
ISO‑grade monitoring. You track moisture levels in wood, curing times for concrete, and weld integrity on steel frames.
-
Batch testing. A single failed test leads to immediate correction, preventing thousands of faulty units.
-
Less waste. Off‑site production generates 60% less construction waste. You cut disposal fees and environmental impact.
These factors reduce rework and defects, meaning fewer change orders and on‑site surprises. Your project stays on budget.
Prefab Homes Financing and ROI
Decision‑makers often worry about paying for new technology. Prefab Homes offer attractive financing structures:
-
Factory‑backed loans: many modular housing suppliers partner with banks to fund off‑site production.
-
Staged payments: pay only as modules complete key milestones—foundation, shell, interiors.
-
Faster break‑even: shorter build times let you lease or sell units earlier, accelerating cash flow.
A typical mass housing project financed over 3 years with a 12% interest rate shows an internal rate of return (IRR) 2–3 points higher than traditional builds, thanks to lower upfront costs and quicker revenue generation.
Conclusion
If you lead a mass housing project, consider how Prefab Homes can slash costs and speed delivery. Reach out to Karmod Nigeria today for a free, detailed cost estimate. Our team handles every step of offsite construction, logistics, and on‑site assembly so you avoid surprises and stay on budget.
To request for price quotation simply contact: +234(0)700-111-1112 or send an email to sales@karmod.com.ng
info@karmod.com.ng